Precast Concrete vs Cast-In-Place vs Tilt-Up

In a previous blog, we’ve outlined the differences between precast concrete and other, more traditional construction methods. But how does precast concrete compare to other concrete construction methods? As an industry leader in precast concrete, High Concrete specializes in a durable, sustainable, and efficient building material.
Throughout this blog, we’ll highlight each construction type and some advantages and disadvantages for each. After reading you’ll have a better understanding of precast concrete vs cast-in-place vs tilt-up.
What Do These Methods All Have In Common?
Since all of these methods are created from concrete, there will be some similarities. All of these methods are relatively sustainable in nature since concrete is made from natural resources and can use recycled material in the concrete mix.
And although some methods are more durable than others, concrete structures can withstand the test of time. Where some buildings will start to deteriorate in the presence of moisture, concrete will only strengthen.
The Process of Cast-In-Place Vs Precast Concrete
Cast-in-place concrete is poured on-site and will generally take up to 28 days to be ready, or cured. After this period of time, the concrete will have its full strength and be ready for installation. Because of this, cast-in-place does have a relatively longer installation time compared to precast concrete.
Although precast concrete also takes time to cure and be ready for use, the process is within a precasting facility so it’s actually much faster. Typically, precast concrete is cured within 48 hours of being poured. Within this environment, there is also a lower chance of error and prolonged timelines.
Cast-in-place can be used to create multiple aspects of your structure including the foundation, walls, and beams. The process of creating these slabs and elements is very labor-intensive and time-consuming. Workers have to pour the ready-mix concrete either by truck, concrete conveyor, or even manually from a wheelbarrow.
The controlled environment of precast concrete allows for a systematic and efficient process. Precasters specialize in a specific part of the process and have more control over the production so there is less risk of error and longer timelines.
With cast-in-place concrete, you have multiple steps to create a finished product. Cast-in-place is only the first step. Then you have to assemble and install the pieces, consider design features on the exterior, and then add windows and doors to the structure.
Precast concrete eliminates some of these extra steps and transports panels that are ready to install and then use shortly after. If you’re looking for stone, terra cotta, or granite, precasters can apply these features prior to pouring. Along with this, our panels can include full insulation and windows already in place.
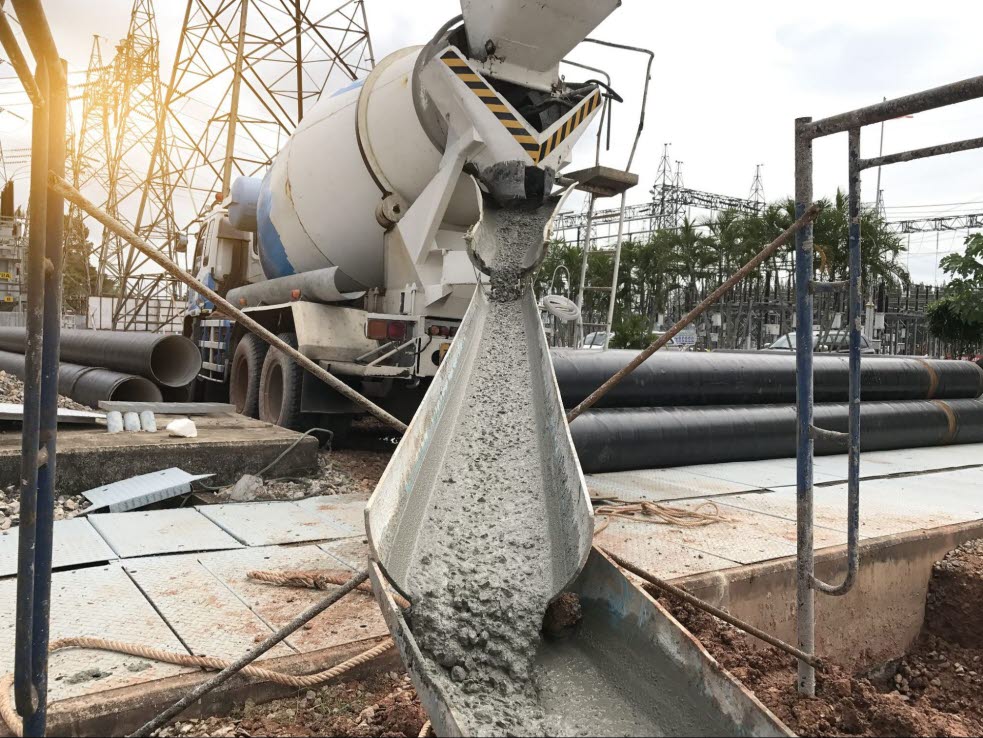
Advantages & Disadvantages of Cast-In-Place Concrete
There are advantages to cast-in-place concrete vs precast concrete. Since it’s constructed on-site, these concrete slabs are best used for the heavier elements of your building. For example, the foundation of your structure may be harder to transport from a precaster’s facility.
Both precast concrete and cast-in-place concrete are very strong building methods. They are both resistant to seismic damage such as earthquakes, floods, or other natural disasters. Also, concrete is relatively inexpensive compared to other construction materials.
Across the board, any material that requires a lot of on-site construction is going to have disadvantages compared to a material that is produced off-site. You’ll have to think about labor, material deliveries, and weather conditions. All these factors can cause issues for your building project.
Cast-in-place construction is a very time-consuming process that involves high amounts of labor. First, they need to place the framework, then place the reinforcements, and finally pour the concrete. Then, you’ll need to wait for the concrete to set and cure. Only then will you be able to start constructing your building.
How Does That Compare to Tilt-Up Concrete?
Now, we’ll compare tilt-up construction vs precast processes as there are quite a few differences between the two.
Tilt-up construction is used to build the exterior walls of a building. Tilt-up panels need to be cast in a mold, on-site, horizontally. They are then lifted by a crane and put into place. The installation process is relatively quick compared to cast-in-place, but you’ll still need to account for the time it takes the concrete to cure and strengthen.
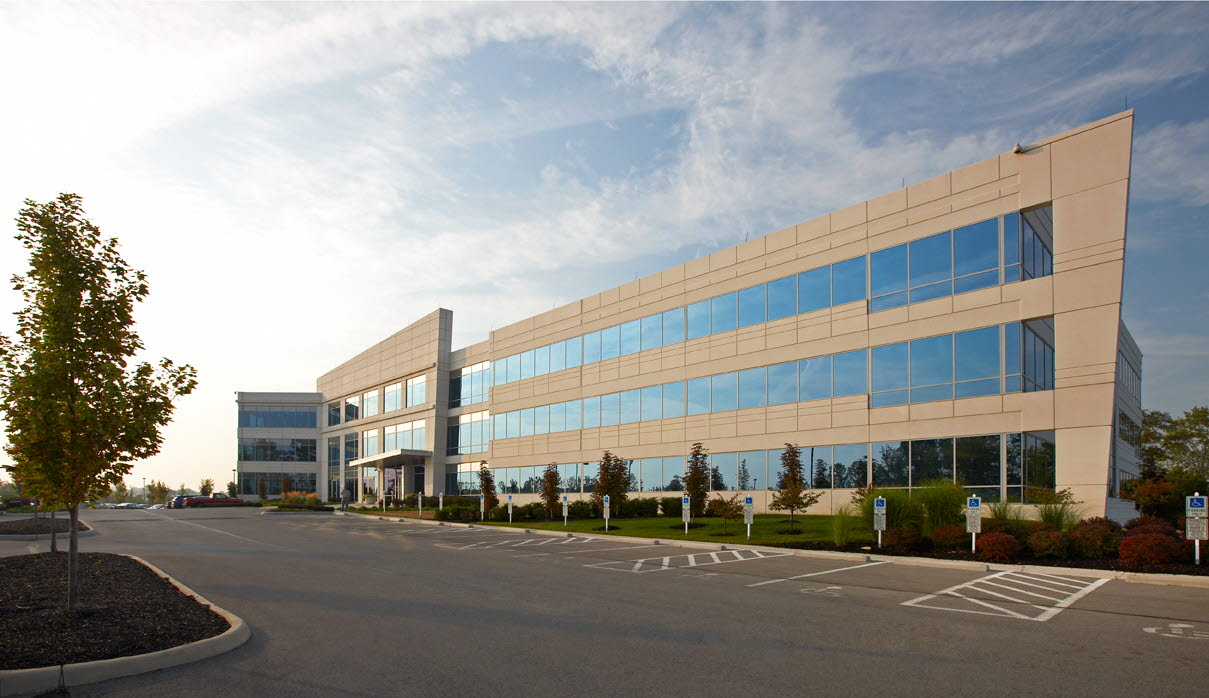
Tilt-Up Panels vs Precast Concrete Panels
Tilt-up panels have grown in their capabilities, but for the most part, these buildings will need to be fairly simple compared to the multiple possibilities of using precast concrete panels. Meaning, it will likely need to be a rectangular, industrial shape. Although this is what some industries are looking for, it doesn’t give the same design flexibility as precast concrete panels do.
In comparison, precast concrete panels can be customized and fabricated to your specifications. Precast panels are also able to be produced year-round so you can expect lower costs and quicker timelines.
Both tilt-up panels and precast concrete panels can be load-bearing, which means they effectively transfer weight from the roof, floor, and walls. Load-bearing walls typically eliminate the need for additional columns within your structure so you can maximize the interior space.
We’ll go into greater detail about the strength of precast concrete later in this blog. Comparing tilt-up construction vs precast, you’ll see that precast is a more durable building material. Typically, psi levels of tilt-up panels are around 4,000 while a precast concrete panel has a psi level of at least 5,000 but sometimes greater.
The psi level helps indicate how much weight each square inch can hold. So, generally, precast concrete can hold more weight compared to tilt-up panels. Because of this, you’ll expect to see less long-term maintenance required for precast concrete panels.
The Disadvantages of On-Site Construction
As previously mentioned, both cast-in-place and tilt-up concrete require much more on-site work compared to precast concrete. This is the biggest difference between precast concrete vs cast-in-place vs tilt-up.
More time on-site means there is more labor needed and a higher risk of delays and injuries. Specifically, for concrete, colder climates make it harder for concrete to cure or strengthen. Because of this, there are times that a project is delayed because of weather conditions.
With everything that goes on within a construction site, the overall quality of control is decreased. Factors such as weather, humidity, potential contaminations, and temperatures all fluctuate the curing time and create a risk for your final product.
Costs on-site are not as stable as costs for a project within a controlled environment. Your labor could fluctuate, or you could have unforeseen logistical delays. When this happens, it will negatively impact your project budget.
You should also consider how on-site construction disrupts the communities around it. Whether that means sidewalks and streets are closed, louder noises, or increased dust, your interruptions affect more than just your project and workforce.
Strength of Precast Concrete
Although compared to traditional methods, concrete as a whole is a stronger option, precast concrete comes out on top as the strongest type among the three. Because precast concrete is created and processed in a controlled environment the factors mentioned above that typically reduce quality control, are not an issue.
Typically, precast concrete uses rebar to strengthen the panels. This makes precast concrete have incredibly strong tensile strength and durability over time. To ensure the strength, precast facilities will perform a series of stress tests prior to delivery and installation.
Precast concrete can use CarbonCast panels, which allow for a stronger and thinner, lighter material. These grids are made from an epoxy-coated composite, carbon fiber. CarbonCast, or C-GRID, has a tensile strength that’s four times higher than steel reinforcing.
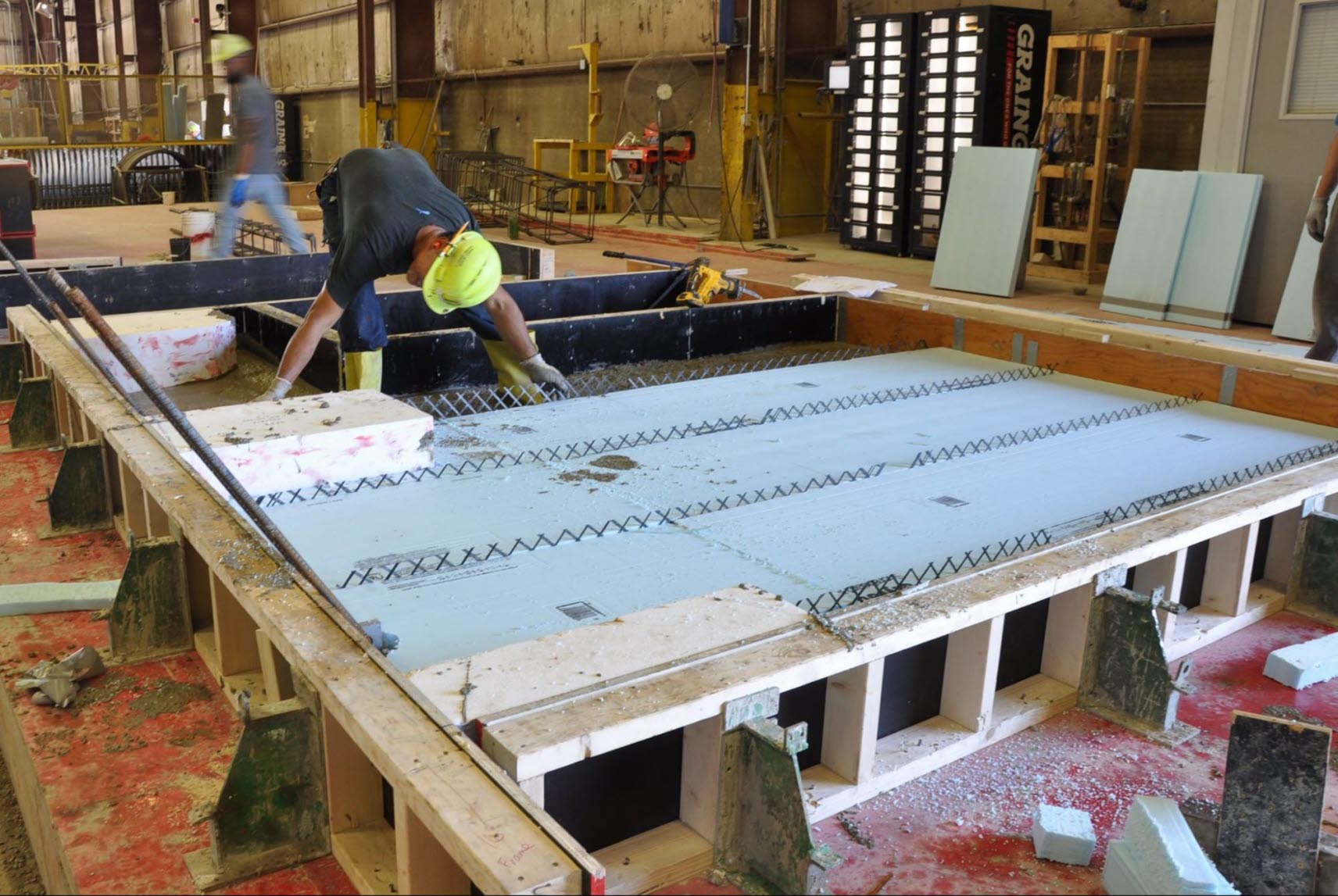
Thermal Efficiency & Insulation
For both cast-in-place and tilt-up construction, the thermal efficiency depends on the insulation placed within the backup wall. This will make your wall thicker and heavier and is an extra step in your construction process.
Without insulation, concrete has a relatively low R-value. So if you’re using this building material for an office space, educational institute, or a building where people will regularly be working inside it, it’s best to make sure you’re using insulation.
When comparing precast vs tilt-up and cast-in-place, thermal efficiency is achieved as a natural step in the construction process. Precasters also have the ability to add continuous insulation to your panels wherever possible.
Effective thermal efficiency provides a great return on investment and savings down the road. It will keep your inhabitants comfortable within the space or allow you to better control the temperatures for specific products. Ultimately, precast concrete panels help you save up to 25% on heating and cooling costs.
Choose a strong, durable building material for your next building project.
